Electric Vehicle Motors And Controllers
Topic: Electric Vehicle Motors And Controllers
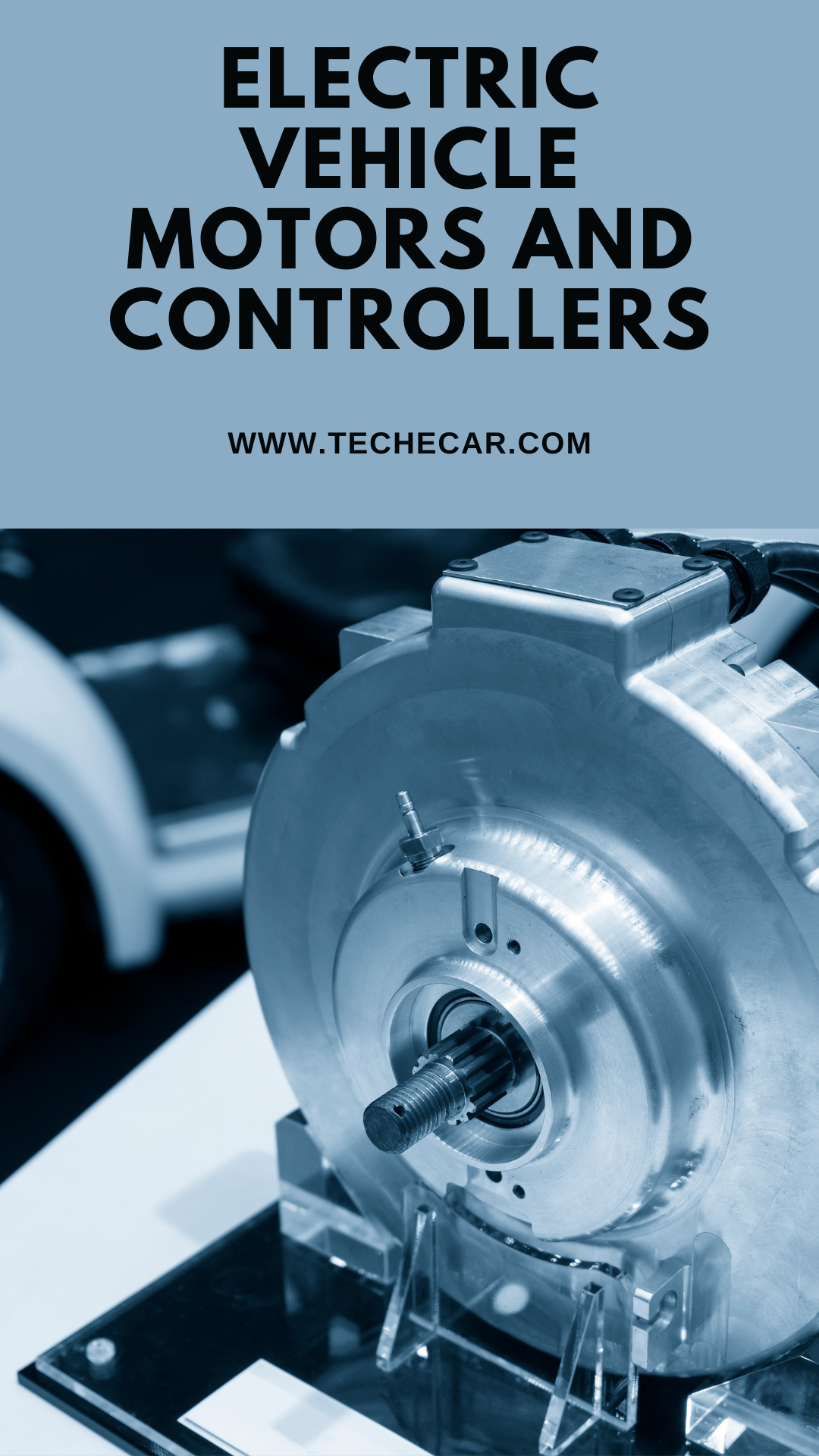
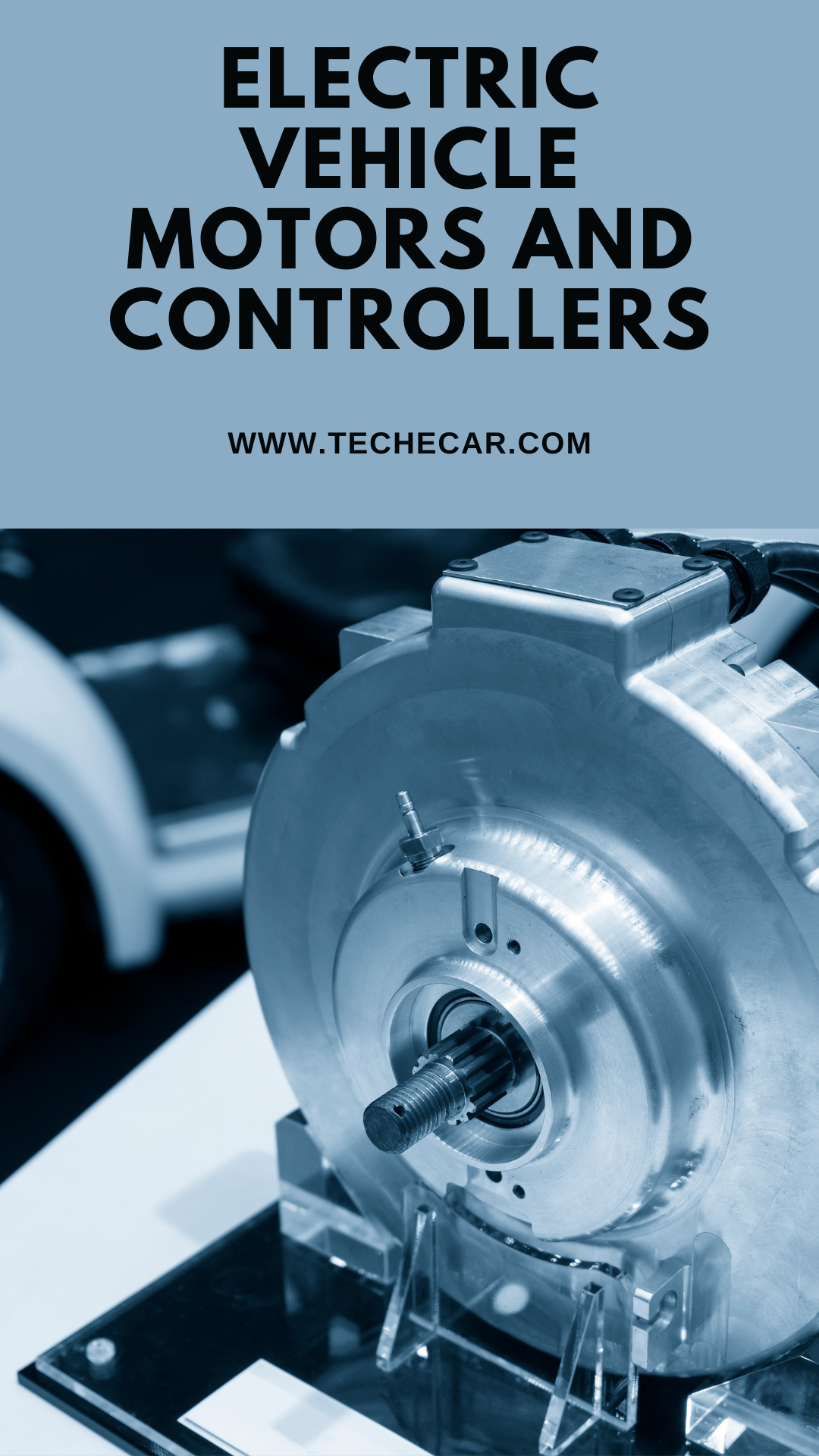
Electric Vehicle Motors And Controllers
Motor Controller for Electric Vehicles
An electric car’s heart is made up of the following components:
The controller aids in the operation of the motor. Electric vehicular motors typically require a commutation driver (similar to DC machines). Vehicle motors, typically BLDC, lack a brush and commutator assembly for this purpose.
The intrinsic controller is in charge of this. The supplied DC will be transformed to a pulsed waveform in the driving circuit before powering the vehicle motor.
The controller transfers power from the batteries to the motor. The accelerator pedal connects to a pair of potentiometers (variable resistors), which provide the signal that instructs the controller how much power to send.
The controller can supply zero power (when the car is stopped), full power (when the driver presses the accelerator pedal down), or any power level in between.
The controller may get 300 volts of direct current from the battery pack in an automobile. It transforms it to a maximum of 240 volts alternating current, three-phase, to power the motor.
The controller’s role in a DC electric vehicle is straightforward. Assume the battery pack comprises 12 12-volt batteries connected to provide 144 volts. The controller receives 144 volts of direct current and controls its delivery to the motor.
The work is a little more complicated in an AC controller, but the concept is different. The controller generates three pseudo-sine waves. It accomplishes this by pulsing the DC power from the batteries on and off.
In an AC controller, the polarity of the voltage must be reversed 60 times per second. As a result, an AC controller requires six sets of transistors, but a DC controller requires only one set. Each phase of the AC controller requires one set of transistors to pulse the voltage and another set to reverse the polarity.
A high-speed BLDC motor controller is developed for electric bikes and scooters, with a powerful and sophisticated microprocessor, up to 40000 electric RPM, compatibility with 60 degrees or 120 degrees Hall position sensor, and support for any brushless motor poles.
Electric Vehicle Motors And Controllers
Electric mobility is increasingly replacing traditional ICE-based power trains in automobiles. Electric trains are more energy-efficient and environmentally beneficial. Advanced motors and motor controllers are responsible for the performance and efficiency of electric power trains.
These motors are much lighter and more efficient than conventional motors, and they require a motor controller to function.
What is the function of a motor controller in an EV?
A motor controller combines power electronics and embedded micro-computing elements that efficiently converts energy stored in an electric vehicle’s batteries to motion.
The cover graphic is a simplified block schematic of a popular electric three-wheeler vehicle. As can be seen, the motor controller is the main component that controls the energy flow to the motor.
Throttle, brake, and forward/reverse control switches are connected to the Motor controller, which processes the commands from these inputs and precisely controls the speed, torque, direction, and consequent horsepower of a motor in the vehicle.
Aside from moving energy from the battery to the motor to provide acceleration for the vehicle, motor controllers may also return energy from the motor to the batteries, allowing electric vehicles to brake more effectively than a basic mechanical braking system.
This technology, known colloquially as “Regenerative Braking,” further aids the electric vehicle’s range by storing energy back in the batteries at each occurrence of braking.
A motor controller’s components
The system’s heart is a microprocessor with embedded firmware that allows the Motor controller to perform its functions.
The power electronics section is represented by the power elements block, which is a bidirectional power converter. It may transfer energy from the battery to the motor and vice versa.
The input interface block connects the other car electronics and communicates with the motor controller.
The sensing/protection block measures all system characteristics such as the battery, current, motor speed, current, etc. The motor controller closely monitors and precisely controls all of these factors. Any malfunction detected in the system will activate self-protection, protecting the vehicle’s safety and its passengers.
One of the most significant components of the motor controller unit is the communication block, which allows the motor controller to share data with external systems.
Through the communication block, the motor controller can send and receive data. The future of mobility is shifting toward shared and self-driving automobiles.
A motor controller and an electric power train are better candidates for providing shared and autonomous mobility due to their ability to share data and synchronise with external systems in real-time.
Motor types and controller applications in electric cars
The controller is the Electric Vehicle’s Carburetor; the requirement for a controller emerges when an electric vehicle operates with a BLDC motor. Before we go into the necessity of a controller, let’s first learn about the many types of motors found in electric vehicles.
The various types of motors found in electric vehicles:
- The motor in the DC Series (Brushed DC Motor)
- BLDC (brushless DC) motor
- PMSM (Permanent Magnet Synchronous Motor)
- Induction Motor with Three Phases
1. DC alternating current motor
The DC series motor has a strong starting torque. The simple speed control and great load-bearing capacity make this an excellent choice; however, the maintenance for these motors is considerable because they include brushes and commutators, but the Indian railways still use this motor.
2. BLDC inverter motor
Because there are no brushes or commutators in these motors, they are highly efficient and require little maintenance. These are more advanced DC series motors. Because BLDC motors have lower losses than others, they are the most commonly utilised motor for electric cars.
3. PMSM (Permanent Magnet Synchronous Motor)
The main difference between it and a BLDC motor is the back emf, which produces high torque and is employed in cars and sports vehicles.
4. Induction Motor
Tesla utilises this type of motor because, unlike other varieties, it has little torque yet can tolerate all environmental conditions.
The Induction Motor
In our vehicle, we use BLDC motors, which do not have brushes or commutators. As a result, we require a device to connect with the motor, which necessitates the employment of a controller. The controller is a device that regulates the speed of the motor and provides a signal to it. In electric vehicles, the usage of a controller is critical for controlling and regulating the vehicle’s speed, charging, and all other controls.
Design of an intelligent controller for an electric vehicle
Abstract: In some electric vehicles, the power supplied by the battery is direct current (DC), which is incompatible with operating a variable-speed direct current motor.
An electronic power converter converts the battery power to the appropriate regulated supply for the motor. The control system determines the precise nature and timing of the current and voltage waveforms delivered to the motor.
At the shaft, the motor turns electric power into mechanical energy, then used to drive the wheels via an appropriate transmission/speed reducer system. An electric vehicle’s torque and power requirements are unusual among variable speed drive applications.
The appropriate torque/power vs speed characteristics are critical for the drive to retain high efficiency throughout a wide range of torque and speed. Motors must be linked to work at a specific voltage and are sensitive to fluctuations in that voltage.
The voltage in an electric car is determined by the battery’s state of charge and the load current. Both of these causes can cause a 20% change in voltage. Thus, the motor must handle these changes in supply voltage.
The torque scaling and speed scaling necessary for transmission speed decrease are the two approaches to scaling a drive. Because of the change in reduction ratio, speed scaling would need the usage of a transmission/speed reducer. The primary goal of this research is to create a fault-tolerant fuzzy logic controller.
The fuzzy logic controller (FLC) increases the initial torque necessary for an electric vehicle drive while maintaining variable speed characteristics and good efficiency. A simple block diagram is provided to illustrate an efficient gear-changing algorithm.
Electric Motor Controller
Motor controllers are electronic devices that control the operation of an electric motor. Motor controllers are devices used in conjunction with switchboards or VFDs to regulate the operation of the prime mover in artificial lift applications.
Motor controllers frequently comprise a manual or automatic means of starting and stopping the motor, choosing forward or backward rotation, speeding up or slowing down, and controlling other operating parameters.
Furthermore, motor controllers can protect the artificial lift system by regulating or restricting torque and defending against overloads and errors. Many motor controllers have extra features such as data gathering and logging and application-specific control logic.
People Also Ask:
What does an electric motor controller do
Motor controllers are electronic devices that control the operation of an electric motor. Motor controllers are devices used in conjunction with switchboards or variable frequency drives to control the operation of the prime mover in artificial lift applications.
- The motor in the DC Series. Back in the 1990s, it was a popular motor.
- Aether Scooters employ Brushless DC Motors (BLDC).
- PMSM (Permanent Magnet Synchronous Motor) in Toyota Prius.
- Induction motor with three phases.