DC DC Converter Electric Vehicle
Topic: DC DC Converter Electric Vehicle
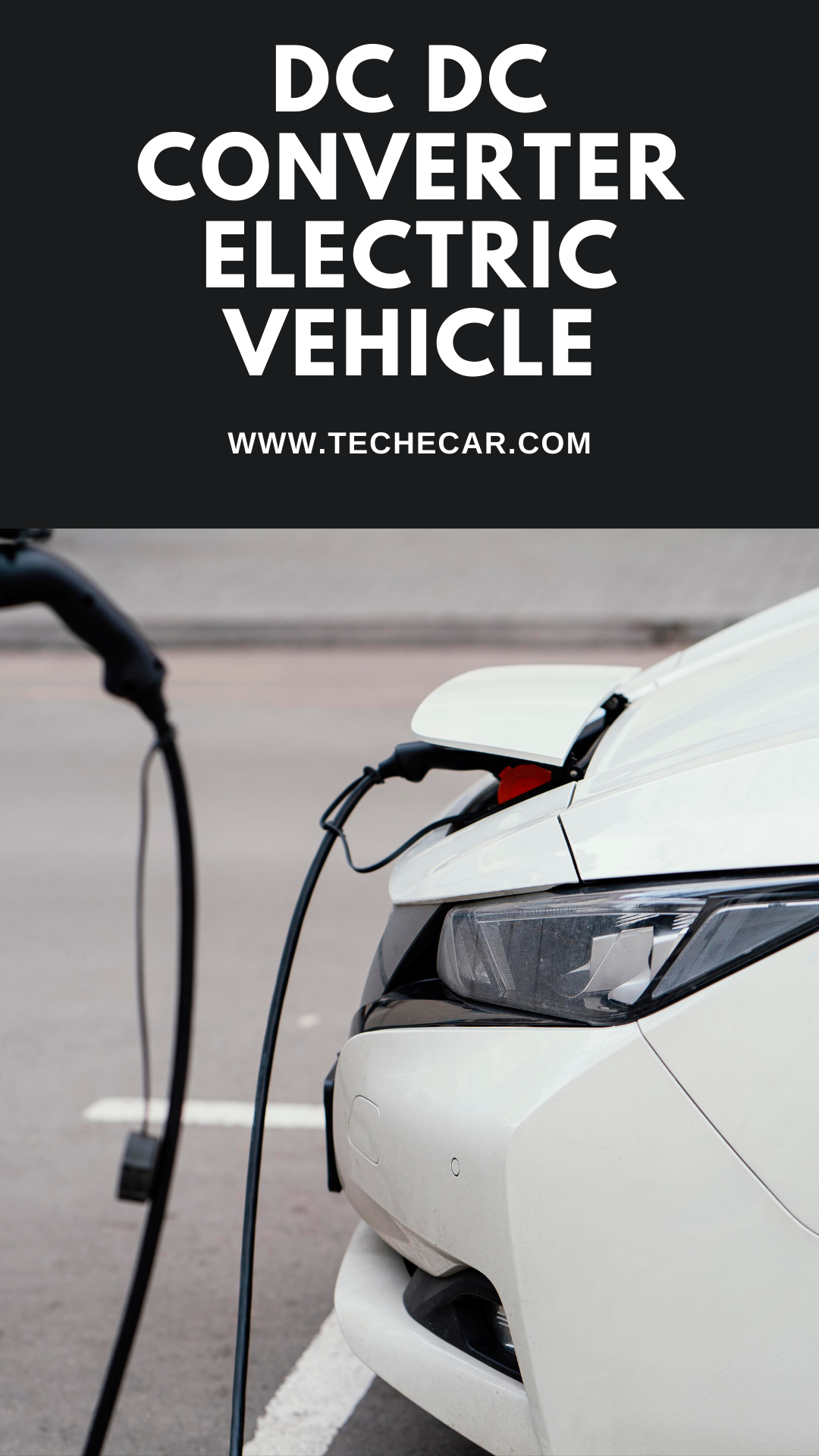
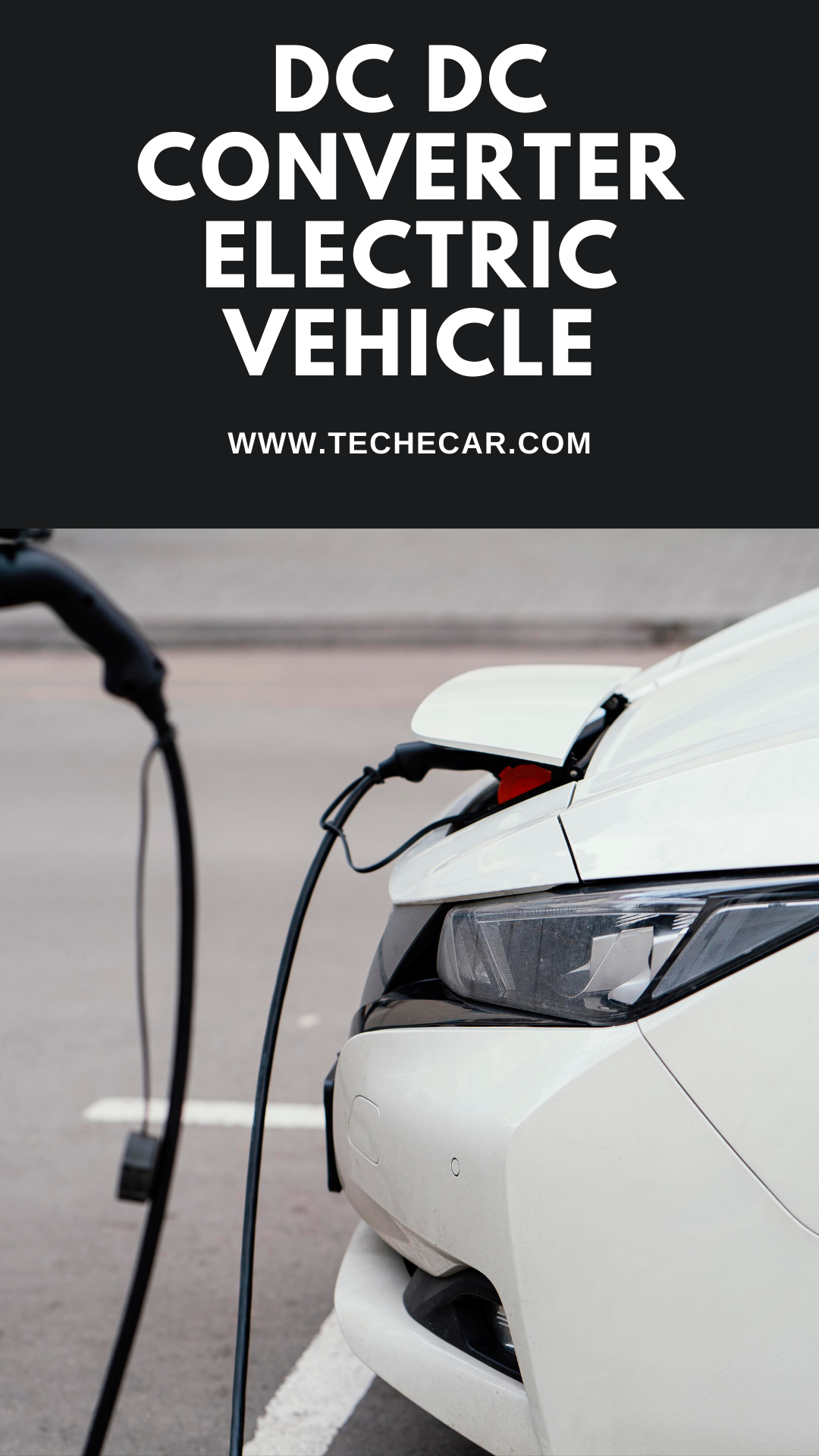
DC DC Converter Electric Vehicle
The battery in every electric car generates a specific voltage.
We need to add another device to the signal path because this voltage may not be suitable for the numerous devices being powered. Modern electric vehicles would not be conceivable without a DC/DC converter.
What is the purpose of a DC/DC converter?
DC/DC converters come in various shapes and sizes, but they all perform the same basic purpose. There are two types of step-up converters: those that take in low voltage and transform it into high, and those that take in low voltage and change it into high.
DC voltage from an electric vehicle’s batteries can range from a few hundred volts to several thousand volts. However, the voltage needs of the electric components inside the car vary, with the majority operating at a significantly lower level.
The radio, dashboard displays, air conditioning, and in-built computers and displays are all included here.
The voltage required to power a DC motor in an electric car can be up to three times delivered by the battery in these vehicles. Using the proper converter, we may eliminate the need for a bulkier, more cumbersome battery.
In electrical engineering, DC/DC converters are a sub-category. Ohm’s Law dictates that there are numerous ways to do a task, all of which adhere to its principles.
Simplified step-down converters might generate a series of on-off pulses and then smoothen this using a combination of inductors and capacitors to produce an output DC signal that has constant current and a voltage determined by the duty cycle (that is, how long it takes for “on” states to “off” states).
What’s the difference between AC/DC and DC/DC power supplies??
The plugs generate an alternating current that fluctuates between positive and negative potentials in your home. There is a 230-volt supply in the United Kingdom, with a 50-hertz frequency (the rate at which the current changes direction).
At 120 volts and a somewhat higher frequency, the voltage is half that in the United States. Direct current, not alternating current, powers most of your home’s appliances. As a result, a rectifier box will be included in the package.
The input signal is routed through a sequence of diodes that clip the negative component of the signal, much like a step-down DC-DC converter. It can then be smoothed using a mixture of inductors, capacitors, and resistors to achieve the desired voltage.
Car converters: electric vs traditional?
The starter motor on a traditional internal combustion engine is very different from the starter motor on an electric automobile. It’s easy to get the 12 volts they need from the car’s battery.
An inverter installed in an automobile can run electrical items that require power from the grid. With this device, passengers may run televisions, Blu-ray players, and game systems in the car as if they were plugged into a power socket.
Running an inverter should be approached with caution for several reasons. They can quickly drain the battery if utilised when the car is not operating. Additional stress could be placed on a vehicle’s alternator by these devices.
A 5 volt USB port with a cigarette lighter adapter can be used to charge many of today’s latest electronic devices. As a result, the cost of an inverter is difficult for most drivers to justify.
DC DC Converter Electric Vehicle
Specifically.
Electric and hybrid vehicles of the modern-day use battery voltages ranging from 300 to 400 volts, with some even going as high as 800 volts, increasing power while also limiting the amount of current flow and cabling required.
As a result, a technique of converting these voltages to lower or sometimes higher levels efficiently is required because these voltages do not suit all of the electrical loads inside the vehicle. DC-DC converters play a key part in this process
High voltage batteries, used in all-electric and hybrid vehicles, contain auxiliary power modules (APMs). One reason is that a low-voltage alternator can be driven directly from the inverter’s output, rather than utilising the inverter’s high voltage output to power an external motor and belt drive.
There are two types of DC-DC converters: bringing high voltages down and converting between different voltages at the low end, both of which are functionally equivalent.
Battery voltage is often reduced to 12 V by a vehicle’s main DC-DC converter for common automotive loads such as headlight, window motor and pump operation. Power steering systems, for example, may require 42 V, whereas other loads require output voltages between 12.5 and 15.5 volts.
A practical limit of 7.4 kW is considered to be reached by some onboard chargers (OBCs) that can handle more than 6 kW; nevertheless, power outputs range from 250 W to 3.5 kW.
Functional safety requirements for converters are increasing due to critical loads on the low-voltage side, such as steering, while reliability standards are also increasing due to car OEMs’ desire to reduce the size of the low voltage battery.
To start a hybrid car or supply backup power, APMs can also convert a voltage upwards, which requires a bidirectional capability. In mild hybrids, this combination is common, converting between 14 and 48 volts.
What do you get when you open this box?
Step-down converters have a variety of components, including transformers that reduce input voltage and capacitors that store energy, semiconductor switches that control the output voltage and capacitors that filter the output.
The digital control logic implemented in devices such as FPGAs is also included because a lot of computation is necessary to fully use the enhanced switching frequencies provided by new semiconductor technologies.
These components have to be integrated and packaged compactly while minimising thermal losses to keep the temperature down. Heat loads become increasingly concentrated as the converter gets smaller, making it more difficult to extract heat effectively.
Vehicles are subjected to a wide range of rigorous working conditions. They must withstand the weight, size, efficiency, dependability, electromagnetic compatibility and high voltage isolation required for safety.
According to this expert, customer demand for larger power densities, according to a professional interviewed for this article, means that switching frequencies will need to be significantly raised.
There are fewer switching cycles with higher switching frequencies. This means that other converter components, such as the magnetics of the transformer, in particular, can be reduced in size because they don’t have to store the power for so long.
Aside from pre-charging, DC-DC converters are emerging to serve additional functionalities such as powering up high-voltage loads using the low-voltage supply and boosting it to begin.
Another method is active discharge, in which circuits in the converter are utilised to bleed down excessive voltages in other components as the car shuts off. Protecting and communicating with the primary ECU is essential for these components.
Switching power sources
OEMs also want more flexibility in adapting to diverse electrical system configurations from different manufacturers. Thus, this is a hot topic. There is an increasing demand for different output voltages on the low-voltage side, all controlled by intelligent software and equipped with data logging capabilities.
For this reason, engineers strive to make DC-DC converters as tiny as possible while maintaining high efficiency to minimise their impact on the overall architecture. As electric actuators continue to replace hydraulic and pneumatic systems, they must service the increasing number and variety of electrical subsystems.
We spoke with a specialist supplier who offers a wide range of products, ranging from a 1.9 kW converter for single-seat race cars and motorcycles to a 10 kW unit for huge SUVs and electric hypercars. The company claims that it weighs just 600 g.
A breakdown of the components of a charger.
Taking a look at the design of an advanced DC-DC converter, a 6.6 kW SiC OBC manufactured by one of the businesses we consulted and comparing important aspects of it to more standard practice is worthwhile at this point.
Capacitor-inductors-inductor-capacitors (CLLLC) series resonant dual active bridge (DAB) converter is its full name.
The converter’s winding structure, series inductor and transformer core arrangement, and heat sink shape have all been designed to minimise core volume, transformer intra-winding capacitance, and eddy current losses caused by flux fringing – the tendency of a magnetic flux flowing through a core to spread out into the surrounding medium near an air gap.
As the frequency increases, the noise level increases in a standard LLC transformer with an inductance of 100 H. However, the primary inductance can be lowered using the CLLLC design even when the frequency rises. Smaller converter components can be made possible by reducing the inductance.
When operating at higher frequencies, the skin effect,’ which causes a concentration of current on the wire’s surface with minimal flow through the core, can also cause losses. As a result, the effective cross-section of the wire is reduced, which increases its resistance due to the eddy currents generated by the magnetic field.
Parasitic capacitance, which is the unintentional storage of electrical charge in components that are close enough to influence one other’s magnetic fields, is another issue. Aside from impairing the effectiveness of voltage conversion, it can also lead to EMI problems.
A magnetic core is prone to alternating magnetisation, generating eddy currents and hysteric effects. The magnetisation lags behind the field, creating it, leading to unwanted heat and poorer efficiency. These core losses tend to outweigh the losses in the windings at higher frequencies.
What’s the worst that might happen?
However, even though current DC-DC converters have proven extremely reliable, they are still subject to failure. If this occurs in isolation, users may be put at risk.
It is also crucial to the operation of an electric vehicle (EV) to have a converter because, without it, there is only a limited capacity low-voltage battery to run all the equipment that doesn’t work via the inverter. As a result, it’s worthwhile to take a closer look at some of the potential pitfalls.
There are many hazardous consequences of overheating. This is why cooling is so important. Insulation and even windings can melt, resulting in catastrophic electrical shorts, but overheating components can also cause more subtle failures such as increased core losses.
This has the additional effect of increasing temperatures, resulting in thermal runaway and a loss of efficiency.
After which, it is possible that the inductance would drop rapidly from 20 to 5 or 6 H, as explained by one expert, leading to loss of voltage and current regulation and possible damage to other components like switches as a result.
Integration of converters into automobile electrical systems might cause complications with load sequencing if various companies manufacture various components on the circuit. The systems integrator must continually look for ways to make sure everything is in sync.
DV/DT, the measure of the instantaneous rate at which voltage changes over time in converters based on IGBT switches, is substantially bigger with SiC transistors. According to an expert, this can be a significant source of noise in cars.
As far as he’s aware, there isn’t any standard for optimising the high-voltage bus DV/DT in terms of uniformity. Vehicle integrators will have to figure out how much
EMI filtering they need until an industry standard is developed; this means that several components fitted in the limited volume available will almost certainly generate EMI.
Design simulation techniques, automated assembly procedures, and components that can operate at greater temperatures have improved reliability. It is also critical to match the load factors of all components to prevent overloading and avoid using any parts with short service lives, such as chemical capacitors.
As long as these safety procedures are followed, service life of at least ten years can be predicted.
Future year’s efficiency
Automotive customers aren’t willing to pay extra for the extra 2% of efficiency that modern DC-DC converters are capable of since it’s too pricey. GaN transistors, on the other hand, could change that.
Creating DC-DC converters for electric vehicles of the future
Anyone who’s looked at buying a car in the last few years will know that things have changed significantly. Diesel and gasoline were the main options available a decade ago.
However, there are now mild hybrid electric vehicles (MHEV), hybrid electric vehicles (HEV), and battery electric vehicles (BEV) to take into account as well. They are all-electric.
Customers see these vehicles as distinct from normal ones because they can’t go as far and require much longer to recharge, and they also have a lot more technology inside. Although many of these adjustments will not be obvious to the untrained eye, they have a substantial impact on the vehicle’s design.
Architectural changes necessitate various power requirements.
A 12V battery powers the electrical components in most internal combustion engine (ICE) cars, which are then recharged by an alternator. Belt-driven components, such as water pumps, power steering pumps, and fans, require no electrical power and thus do not need to be plugged in.
As more people switch to hybrid and electric vehicles (EV), this practice is becoming less common. Electric motors are increasingly taking the place of mechanical ones in modern automobiles (including EVs and even some ICE vehicles).
The smaller, lighter and more dependable new models make more efficient functioning possible. The air conditioner doesn’t need to operate constantly, but a belt-driven pump does, whereas an electric motor-driven pump is only powered when it’s needed.
However, many of a vehicle’s pumps and motors necessitate a considerable amount of electricity — on the order of kilowatts (see Figure 1 below). Due to their high power consumption, these applications cannot be powered by the 12V battery, often found in most automobiles and gadgets like heated seats.
The design concerns and difficulties of EV bi-directional DC-DC converters
Most vehicles use a 12V system for lower-power applications to keep the two power systems separate. In contrast, a 48V system is used for higher-power ones (those requiring motors and heating elements). This configuration is common in today’s vehicles.
The 48V bus is being created with a number of the most cutting-edge vehicle features, including active chassis management, adjustable suspension, and electric superchargers/turbochargers. Engine starting in ICE vehicles is made easier with the 48V bus’ ability to accommodate this feature.
A bi-directional DC-DC converter serves as the bridge between the two voltages in these mixed voltage systems. Both the “buck” and “boost” converters in this crucial subsystem can be used to charge either battery from the other.
There were two different DC-DC converters utilised in the early stages of this technology. As a result, external components (such as inductors and capacitors) can be employed for both the stepping-up and stepping down conversions.
Reduced size and weight lead to increased efficiency and a lower production cost for the vehicle. The bi-directional DC-DC converter can integrate energy from both systems to maximise power output when the current draw is at its highest. For example, when starting the car.
As a result of the extra-low voltage (SELV) used in automotive systems, galvanic isolation isn’t necessary, which is one of the reasons 48V was chosen. As a result, non-isolated bidirectional DC-DC converters are more common.
An MDIBC (multidevice interleaved bidirectional DC-DC converter) is a frequent alternative to an isolated MDI.
A sealed lead-acid (SLA) battery provides the 12V power, while a supercapacitor or a battery/supercapacitor combo can provide the 48V power needed to deliver high current peaks.
Reduced input ripple can be achieved by interleaving the gate drive signals in the MDIBC depicted. While it may seem impossible, it is possible to achieve acceptable input and output ripple levels by simply using lower-cost passive components.
Wide bandgap (WBG) semiconductors are increasingly being used, allowing for higher operating frequencies and smaller passive components.
The DC-link capacitor, control circuit, and thermal management are all shared by the MDIBC, which makes it more reliable than many conventional topologies. Because it allows power to flow in both directions, regenerative braking systems can recharge the battery and boost the vehicle’s efficiency and range.
48V systems are subject to these standards.
It’s inevitable that as technology advances, so will the number of standards and regulations that apply to vehicle electrical systems design. Even though several existing standards (such as ISO 7637) cover 12V and 24V and much higher voltages, there is a void around 48V.
There will be a major overhaul of the electrical infrastructure due to 48V. Currents won’t necessarily be reduced because 48V will be utilised to power systems that require greater energy.
As a result, system components such as fuses and relays may be subjected to greater loads, increasing the likelihood of an arcing incident.
System modifications, including replacing mechanical relays with solid-state devices, introducing smart fuses, optimised wiring harnesses, and fault-tolerant features—all leading to completely autonomous vehicles—will be made possible by the switch to 48V.
A single global standard for 48V automotive systems has been established, making it easier and cheaper for automakers to compete in international markets. To coincide with its publication in late 2019, converters conforming to ISO 21780 were made available for purchase.
DC-DC converters in automobiles rely on key passive components.
Passive components play an equally significant part in automotive DC-DC conversion as switching semiconductors like IGBTs and MOSFETs and modern controllers.
Energy storage, filtering, decoupling, and noise reduction are common uses for inductors and capacitors. Passive components often outweigh semiconductors by a wide margin (BoM).
High temperatures, transients, noise, and other risks abound in the automotive industry. An application’s electrical and mechanical properties must be considered in component selection.
Additionally, there will be a wide range of capacitors, including the multi-layer chip capacitor (MLCC), commonly used in smoothing and snubbing applications.
Polypropylene film capacitors, for example, have a high voltage capability and are frequently employed to filter undesirable EMI. There are also self-healing varieties that can be used in automobile applications.
Inductors are also employed in various power applications, from filtering to providing energy storage in buck converters. Saturation and the quantity of current the winding can carry are critical considerations for current handling capability.
Inductors with thick strip-wound copper wire reduce DC resistance and the resulting losses to a minimum. The creation and vulnerability to electromagnetic interference (EMI) in switching applications necessitate shielding.
Common-mode chokes, current sense transformers, and small PCB-mount transformers, all of which are utilised in the drive circuitry of semiconductor switching devices like IGBTs and MOSFETs, are magnetic components are also used in electronic systems.
Connectivity is critical in automotive systems because of modularity and ease of service and repair. The specification of connectors must be carefully considered to avoid losses in the system as currents and voltages increase.
Connectors ‘ mechanical characteristics and heat resistance are critical because of their use in under-the-hood applications, including start-stop systems and electric turbos/superchargers.
Summary
It may not be obvious to many car consumers, but fundamental power architecture is changing even in ICE vehicles. It is becoming increasingly common for hydraulic and mechanical components and other electrical and electronic components to be replaced by 48 V systems.
This method is more efficient and saves money because cabling may be reduced in size and weight.
It’s necessary for the DC-DC converter used to work bi-directionally to recover energy lost when the car brakes and restore it to storage, which extends the vehicle’s electric range.
Choosing components for these DC-DC converters that can survive the increased pressures of 48 V operation (and the harsh automobile environment) becomes increasingly important as voltage rises.
Due to the high degree of electrical/electronic content in modern automobiles, many component makers now produce devices expressly for these new applications, including inductors, capacitors, filters, chokes, current sensors and connections, due to the high degree of electrical/electronic content in modern automobiles.
People Also Ask:
DC-DC converter in electric vehicle pdf
There have been and continue to be major issues with the environment and human life created by the vast number of automobiles in use around the world. Air pollution, global warming, and the rapid depletion of the Earth’s petroleum resources are now major concerns. Conventional automobiles are expected to be replaced by electric vehicles, hybrid electric vehicles, and fuel cell electric vehicles (FCEVs).
- ON Semiconductor’s LM2576D2TR4-5G IC.
- Recom Power’s R1SE-0505-R.
- Traco Power’s TSRN 1-2433.
- Linear Technology’s LT8640EUDC#PBF model number.
- Linear Technology’s LTC3114EFE-1#PBF.